Green steel and intermittency risk
Can the steel industry decarbonise using variable-output wind and solar?
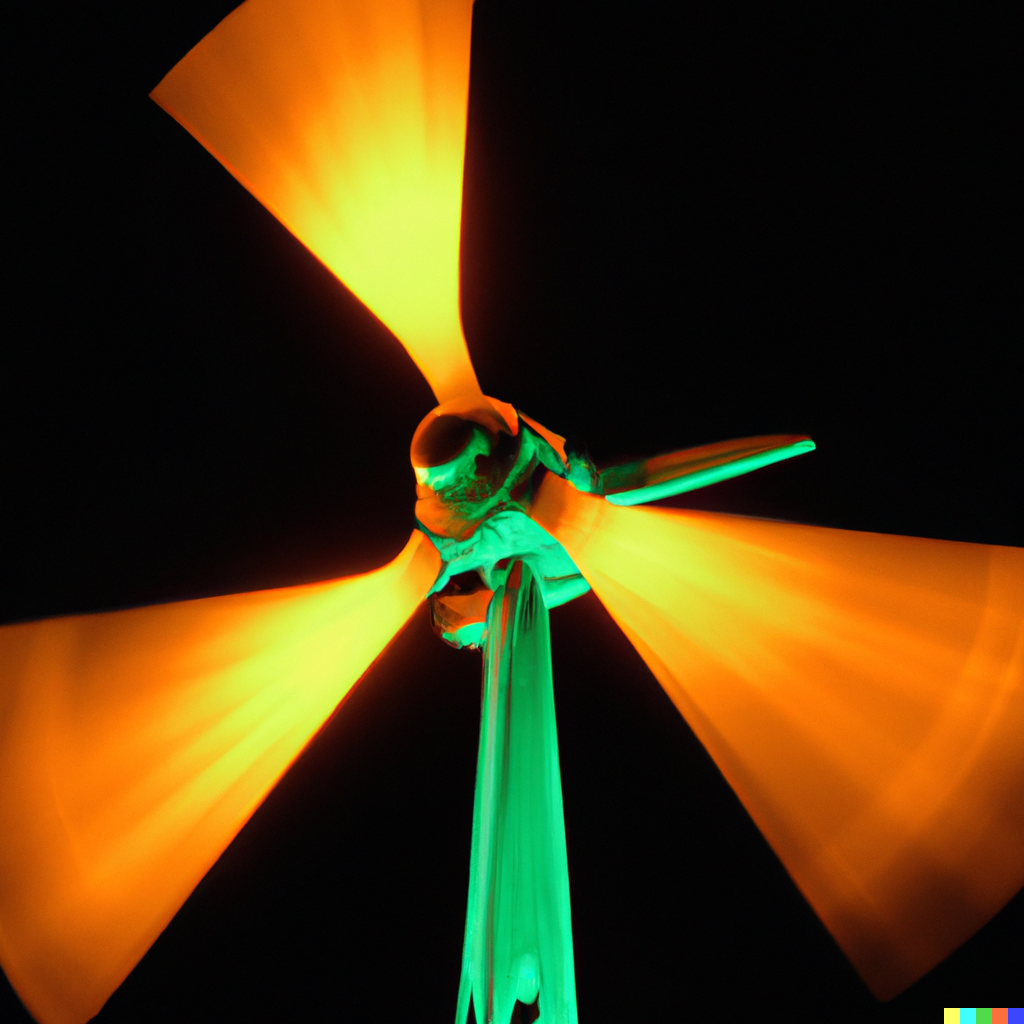
Can the steel industry decarbonise using variable-output wind and solar?
New and improved modelling cuts through the noise to give a clearer view of shifts in risk pricing
DEEP DIVE: How low must LNG prices go to unlock Asian demand?
TTF bull trap turns investment funds into bag holders | EU LNG Chart Deck: 26 June 2025
TTF turns on a dime, but is risk being priced properly? | EU LNG Chart Deck: 20 June 2025